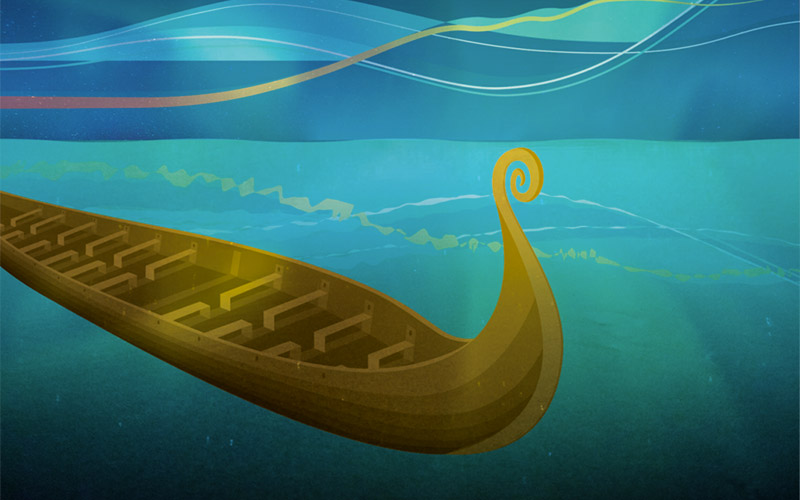
15.09.2023
Sharing important learning from building a CCS facility in an operating plant
It is complex to establish a CCS facility in an operating plant. This is documented in Heidelberg Materials’ and Hafslund Oslo Celsio’s lessons learned reports. For financial reasons, the companies will always prioritize maintaining operations at the industrial facility. Limited space and integration of the CO2 capture plant can present challenges that must be resolved.
Both Heidelberg Materials ( (Heidelberg) and Hafslund Oslo Celsio (Celsio) receive financial support from the Norwegian Government for the establishment of CO2 capture facilities. They are both part of “Longship”, the first industrial CCS chain in Europa. It is a goal for the Government that “Longship” provides learning that subsequent CCS projects can benefit from.
Heidelberg Materials is building a CCS facility at the cement factory in Brevik. Their lessons learned report is based on the experience from the start of the construction project in early 2021 until the end of 2022, when the construction was 50 percent completed. Celsio’s experience report is based on their experience from the start of the construction project, August 2022, until the end of 2022. Thus, Heidelberg has a greater experience base than Celsio, which is also reflected in the reports and in this article.
Celsio will construct a CO2 capture facility in the waste-to energy facility in Oslo. However, in April 2023 Celsio put the carbon CCS project into a “cost-reducing phase”. An updated cost estimate showed that cost increases on i. a. equipment deliveries would have led to the project exceeding the investment limit agreed with the state.
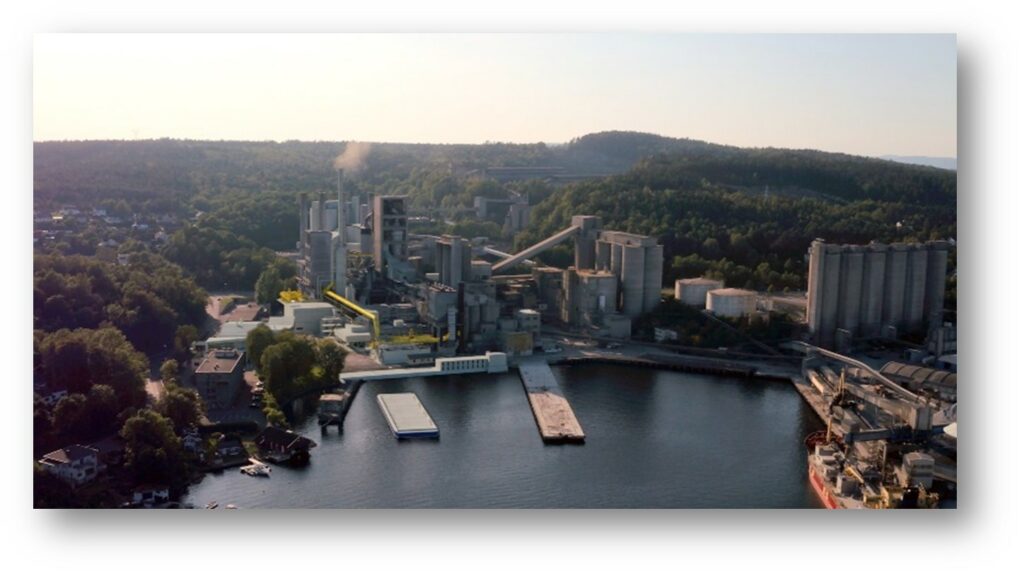
Involvement of the operating organisation
In the Brevik CCS project, the CCS plant is being built quite close to the operational cement factory. Due to the tight interfaces between the two plants, Heidelberg highlights the importance of involving personnel with operational experience from the cement factory in the project development right from the start. For any interface challenge that may arise, it is important to identify and quantify the impacts, communicate any changes and, if necessary, evaluate the design. All known issues must be fully investigated and not deferred to the implementation phase. It is important to have a valid project design already during the FEED study, Heidelberg emphasizes in its report.
Heidelberg acknowledges that the establishment of the CCS facility in Brevik makes the working conditions at the factory demanding for a long time. Nevertheless, there has been very little friction to trace in the operating organisation. “General support from all internal stakeholders is critical. This is only achieved through maintaining an open dialogue with the plant and engaging them early on issues,” writes Heidelberg in the report.
Celsio also emphasizes that future projects will have a lot to gain from involving the operating organization at the plant early in the process, both in planning and implementing the project. Dedicated resources from the operating organization should be included in the project organisation, Celsio writes in his report. ” This is a well-known fact for such projects, but still difficult to achieve in practice in plant organizations where attention and resources are inevitably drawn towards daily operations,” the report states. By actively involving the operating organization in project planning and implementation, they will be able to contribute valuable input that provides good integration between the production plant and the CO2 capture plant. Active involvement strengthens ownership in the operating organisation.
The need for space must not be underestimated
Both Heidelberg and Celsio have experienced that the need for space can easily be underestimated.
Heidelberg writes that space requirement is very an important consideration during the design of the CO2 capture facility. Arrangements must be made for access roads; maintenance requirements and construction considerations must be considered. These requirements must not be underestimated.
For Heidelberg, it has been a great advantage that the facility is located by the sea. This has made it possible to bring in prefabricated components. In addition, a nearby fabrication facility (at Trosvik) has opened for prefabrication of modules that can be moved by barge to Brevik. ” It is rare that such a situation exists, so future CCS projects will need to consider this difference when Brevik is benchmarked against other projects,” Heidelberg writes in the report. Heidelberg also changed the timing of construction of the maintenance center to the very end of the project to have sufficient land available during construction. This does not delay start-up but means that the lease period at Trosvik had to be extended.
Early during the construction phase the Celsio identified that the expected need for rigging space was challenging, and somewhat underestimated. Sufficient rigging area is key for the successful implementation of the project and for the fully operational WtE plant to simultaneously run smoothly. However, there is not an abundance of available land in the proximity of the Klemetsrud WtE plant. Future projects should ensure access to/ownership of sufficient land before the investment decision is made, but also consider that the need for land may be higher than expected, writes Celsio in the report.
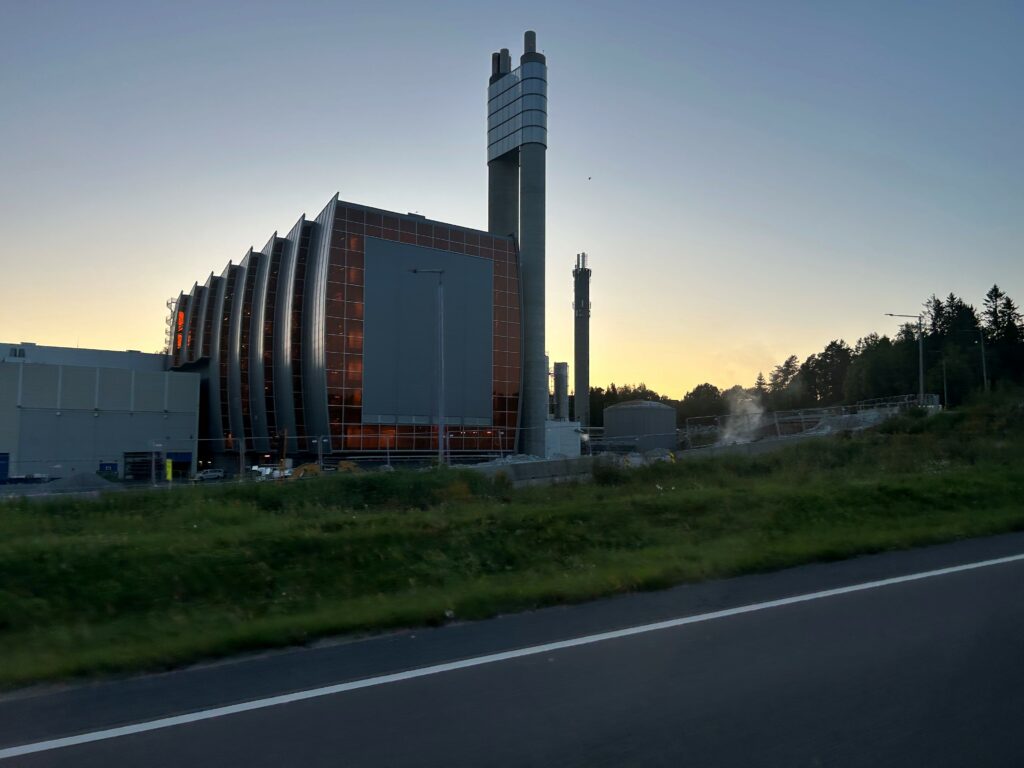
Tight integration presents challenges
The tight interface between the cement factory in Brevik and the CCS plant presents some significant challenges: For example, the close interface between the cement/CCS plant makes it important to consider what to do with excess heat within the cement plant when the WHRU is taken offline suddenly. There is a risk of adverse consequences if the hot flue gas is not cooled. It is possible that the the gas conditioning tower (water spray) may not be able to react quickly enough to cool the flue gases sufficiently. This will be investigated further when the process simulator is operational. Future CCS projects should consider emergency shutdown conditions during the pre-FEED study. Heidelberg’s conclusion is that risk can be reduced by reducing the operating plant’s dependence on the CCS plant as much as possible.
Since the cement industry is not familiar with the operating requirements of a chemical plant, personnel training is required and more specific instructions from the supplier are needed, according to Heidelberg.
Celsio also highlights integration challenges in its report: Since the flue gas interface is complex from a process point of view, it is important to address this topic early on. Both personnel from existing facilities and from the CO2 capture project should be involved, they write.
At Klemetsrud, the energy recovery plant and the CO2 capture plant will be operated from the same control room but operated as two separate plants. The energy recovery plant shall not be affected if the CO2 capture plant is out of operation. However, Celsio acknowledges that this will cause interface challenges that need further investigation. Typical problems are pressure and temperature conditions, emission monitoring, start-up, shutdowns, and emergency situations.
Operation at the plant most important
Celsio recommends developing a detailed master plan before an investment decision, where careful consideration is given to the importance of avoiding impact on the daily operation of the process plant. This is particularly important when the W-t-E facility must be in full operation 24/7/365 during the construction period. In such cases, it is recommended that the project carries out an additional independent study/”construction report”, which assesses how best to maintain operations.
Heidelberg emphasizes planning to ensure that downtimes can be utilized to the maximum: ” Winter repairs/annual outages are very important milestones in the execution, both as opportunities and restriction. They need to be planned very carefully and the key objectives in relation to the project agreed long in advance to capture the most benefits,” writes Heidelberg.