1. General
Norway has a long history of carbon capture and storage (CCS). Gassnova has been working with all stages of the development of CCS since 2005, from R&D to industrial scale. The main goal of our work is to contribute to technology development and cost reductions and enable deployment of CCS through knowledge sharing and experience transfer together with our partners. The Norwegian Full-scale CCS project, named Longship, is a result of exactly this objective.
Through a unique long-term cooperation between the Norwegian state and government agencies, R&D institutions, academia and the industrial partners in the project we have jointly managed to mature and develop CCS technology and a full-scale project that is now ready for industrial deployment. In particular we want to acknowledge Heidelberg Materials Brevik, Fortum Oslo Varme (now Hafslund Oslo Celsio (Celsio)) and the Northern Lights partnership who has put a lot of efforts and resources in sharing their learnings and experience from the development of the projects in a very professional and cooperative manner.
Gassnova’s report on the key lessons learned from the planning of Longship is based on the knowledge shared by the industrial companies involved, our own experience from following up and coordinating the project and also our long history of working with the development of CCS technology.
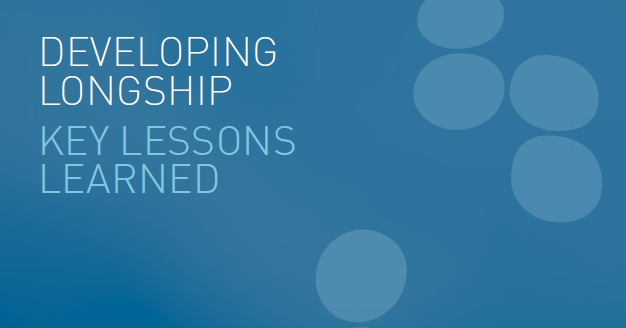
Longship covers the capture of CO2 from Heidelberg Materials’s cement factory in Brevik and from Fortum Oslo Varme’s waste-to-energy plant in Oslo. The captured CO2 will be shipped in liquid form to a CO2 receiving terminal on the Norwegian west coast. From there, the liquefied CO2 will be transported by pipeline to an offshore storage location under the North Sea for permanent storage. The transport and storage part of the project is a collaboration between Equinor, Shell and Total called the “Northern Lights Project”.
On 21st September 2020 the Government proposed to realize the Longship project with the three industrial partners Heidelberg Materials, Fortum Oslo Varme and Northern Lights. The state aid to Fortum Oslo Varme will be given provided that they secure sufficient own funding as well as funding from the EU or other sources. Realization of Longship is subject to approval by the Parliament in December 2020.
This is a first-of-its-kind project when it comes to: the emission sources where the CO2 will be captured; the scalable transport and storage infrastructure ready to be used by other emission sources; and the application of European and Norwegian CCS regulations. The different technical solutions are in operation elsewhere but are put together for the first time to form a complete CCS chain.
Although Heidelberg Materials, Fortum Oslo Varme, and the Northern Lights partnership have received state aid throughout the project development, each industrial partner is responsible for their own project.
Gassnova is a state enterprise owned by the Ministry of Petroleum and Energy (MPE) and has been administering the public funds to the industrial partners through agreements for study of capture, transport and storage of CO2. It has also coordinated the overall project schedule and managed the cross-chain risks and functionality. MPE has been leading the negotiation with each industrial partner on the terms for the state aid for the potential construction and operation of the CCS-facilities.
In a Government White Paper to the Norwegian parliament submitted on 21st September 2020, the Government proposed to launch a carbon capture and storage (CCS) project in Norway. Named ‘Longship’, the project has been developed over the past 6 years and the Final Investment Decision will be taken by the Norwegian Parliament in December 2020.
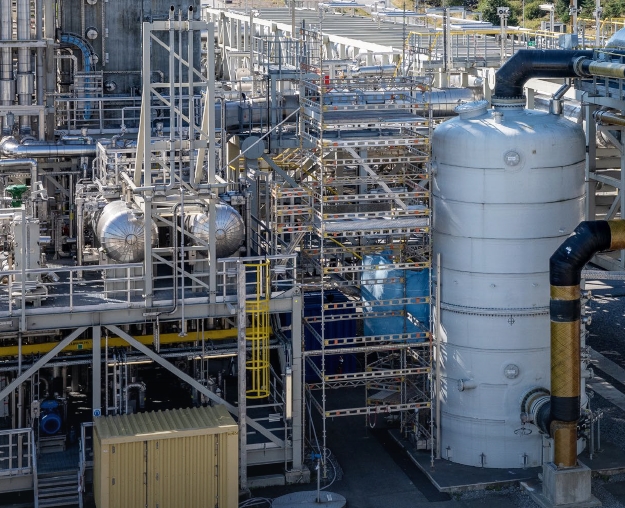
This document sums up what Gassnova considers to be the key learning points from the project up to this point. Although the project has been developed under circumstances that are unique for Norway, the experiences are relevant for the setup and development of other CCS projects. At a glance, these are:
- Developing a CCS chain with CO2 capture, transport by ship and geological storage is technically feasible and safe, but commercially challenging.
- The London Protocol that has been a barrier for cross-border transport and storage of CO2. However, in 2019 the parties to the London Protocol agreed on a temporary amendment allowing export of CO2 for the purpose of storage offshore. Aside from this, no regulatory showstoppers have been identified so far.
- It has been possible to develop the CCS chain with limited use of new technology, and only for the amine technologies used to capture of CO2 there are no fallback solutions.
- Although there are few comparable CCS chains world-wide, experienced and competent contractors and suppliers can be mobilized and the technical know-how is readily available.
- As expected for a first-of-its-kind CCS project, the net cost per tonne for capture, transport and storage is high; for 800,000 tonnes per year the cost is around NOK 1,280, which will decrease with full utilization of the transport and storage facilities.
- The time needed to perform detailed engineering and construct transport and storage facilities based on ships and a greenfield CO2 receiving terminal is approximately 36 months. For a capture plant retrofitted onto an existing industrial plant, this will take up to 42 months.
- Upon approval by the Parliament, Heidelberg Materials and Northern Lights will each enter an agreement with the government providing state aid to the construction and first ten years of operation of the CCS-facilities. Reflecting the balance between risks and opportunities in these agreements, the state will bear approximately 84% and 73% of the expected cost of Heidelberg Materials’s and Northern Lights’ projects, respectively. The government is ready to cover 40% of Fortum Oslo Varme’s cost provided that they are able to secure additional funding from third parties.
This document presents key learnings from the development of Longship from the pre-feasibility study in 2014 up to completed FEED studies and the industrial partners FID’s in 2020. Maximizing the value and availability of “lessons learned” from the Norwegian CCS efforts is part of Gassnova’s mission. The key learnings have been formulated as seen through the eyes of Gassnova as a public “project integrator”, and when the learnings are characterized as “successful”, they must be understood in this perspective: the project has matured to the right level, the industrial partners have taken their investment decisions, and the government is ready to take the FID.
The learnings presented here are primarily related to CCS-specific aspects of the project, indirectly touching upon the public financing. General project experiences are mostly omitted. The aim of this document is not to make firm recommendations, but rather to present central lessons learned to assist anyone who has an interest in developing CCS.
This document is structured around the framework of the project (Chapter 01), as well as the project development itself (Chapter 02). However, it also draws on Gassnova’s wider experience in the develop- ment of CO2 capture technology (Chapter 03).
Glossary | |||
---|---|---|---|
Availability | Fraction of time when a system is operational, assuming that the required external resources are provided. External resources are e.g. production of cement or incineration of waste, and supply of electricity from the grid. | KS2 | External quality assurance of project control basis and cost estimates before FID |
AACE | American Association of Cost Engineers | LPG | Liquified Petroleum Gas |
CCS | Carbon Capture and Storage | LNG | Liquified Natural Gas |
ESA | EFTA Surveillance Authority | MPE | Ministry of Petroleum and Energy |
EU ETS | EU Emissions Trading System | NPD | Norwegian Petroleum Directorate |
FEED | Front End Engineering and Design | R&D&D | Research, Development and Demonstration |
FID | Final Investment Decision | SMART | Specific, Measurable, Achievable, Relevant and Time-bound |
IEA | International Energy Agency | TCM | Technology Center Mongstad |
IMO | International Maritime Organization |
The Norwegian Continental Shelf has a vast capacity to store CO2 in geological formations, and a stable and broad political will to fund CCS R&D has resulted in Norwegian research entities and companies working in the field of CCS for a long time. When the “Sleipner” CCS Project was commissioned in 1996 it was the world’s first offshore CCS plant. More than a million tonnes of CO2 have been stored in the Utsira formation below Sleipner every year since then. In the “Snøhvit” CCS project, CO2 has been separated from raw natural gas at the onshore LNG plant at Melkøya and transported and stored offshore since 2008. Technology Center Mongstad (TCM) is the world’s largest testing facility for CO2 capture technology and was opened in 2012. These CCS operations and the surrounding R&D activities have helped to build trust in the technology among the Norwegian population.
Various Norwegian governments have long had an ambition to realize a full-scale CCS project. There have been attempts to develop CCS at the gas processing plant at Kårstø and the refinery at Mongstad while the current project is based on capture of CO2 emissions from industrial sources.
In developing Longship, the emphasis has been on using the expertise built up over many years through previous CCS projects, TCM and the R&D&D programme CLIMIT.
The Norwegian Government’s CCS strategy was presented to the Parliament in Prop. 1 S (2014-2015). This strategy sums up the state’s broad involvement in CCS activities in Norway and internationally which can contribute to technology development and cost reductions for CCS and describes an ambition to realize a full-scale project.
Although the need for CCS to meet long- term global climate goals has been well documented, IEA and others have for years constantly reported a portfolio of industrial CCS projects far below the identified need, even though technologies exist. Several barriers to commercial CCS investments have been identified. In order to overcome these investment barriers, there is a need for innovation related to business models, policy and regulations.
Industry will not invest in technology with an uncertain future market potential, and policymakers cannot commit to a technology they do not know and whose future industrial interest is unclear. To break this deadlock, an industrial full-scale and full-chain demonstration is needed.
The way the Norwegian project has dealt with this situation is through a public- private cooperation based on trust and stepwise maturation of the project.
Based on the Government’s CCS strategy, Longship has from 2015 been developed in stages with several industrial partners and according to best practices for industrial projects. Early on Gassnova recommended establishing a transport and storage operator that could offer transport and storage services to industrial parties who often do not have the required expertise and resources. The target segment for potential CO2 capture sites is existing land- based emission sources with emissions above 400,000 tonnes of CO2 per year. An important premise for the state is the self- interest the industrial partners have in CCS.
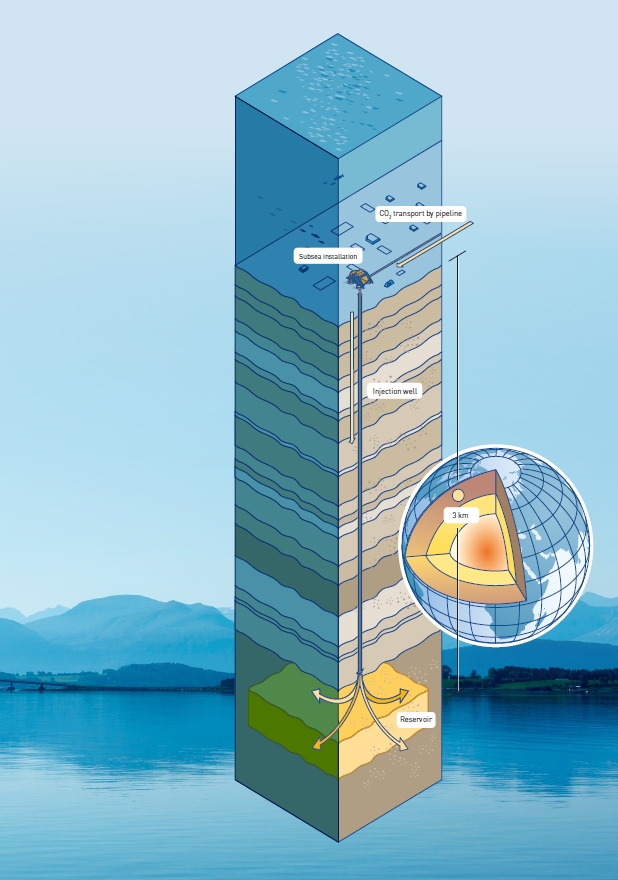