4. Technology qualification
The technical solutions to be used throughout the CCS chain are generally well known. However, technology used to capture CO2 from exhaust gas from combustion or industrial processes is still relatively immature and there are few references to operating facilities of significant size. It has been critical to verify that emissions of potentially carcinogenic substances deriving from the amine solvents used for the capture will be below the allowable limits established by the authorities in Norway. Use of recognized standards for technology qualification has proved useful.
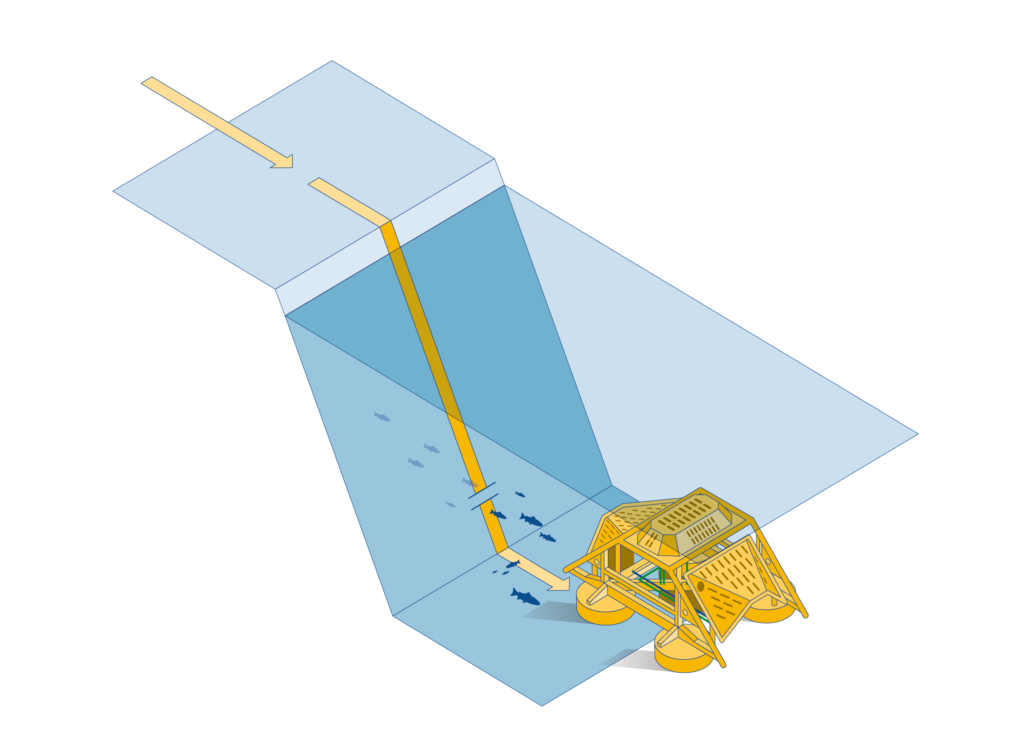
The purpose of conducting a technology qualification is to reduce the risk of implementing technology and evaluate the consequences of underperformance, in a structured manner. This is particularly relevant when the technology is new to the buyer and has few, unknown, or irrelevant reference cases. The qualification should be finalized before the FID in a way that reduces the residual risks to levels that the project owner and end-user consider to be acceptable.
In performing technology qualification, it is advisable to use a recognized standard or practice. This will ensure that all relevant aspects are covered and that the results are displayed in a structured and transparent manner suitable for any independent third- party evaluation.
Through the concept selection and definition phases, Gassnova has required the industrial partners to qualify new or unproven technology elements in accordance with recommended practices from DNV GL, specifically DNV-RP-A203 and DNV-RP-J201.
A systematic approach to evaluating the novelty of the different technology elements in the project is a good starting point for identifying the need for and extent of technology qualification; see Table 3 for an example from DNV-RP-203 (2013).
As indicated in the table, unless a technology is considered proven and well known within the current application area (Category 1 – green colour), there is a need for technology qualification.

Table 3: Technology Novelty Categorization, from DNV-RP-A203 (2013), Table 7-1. Category 1 indicates that there are no new technical uncertainties, while category 2 to 4 indicates that there are new technical uncertainties or challenges. Colours added by Gassnova.
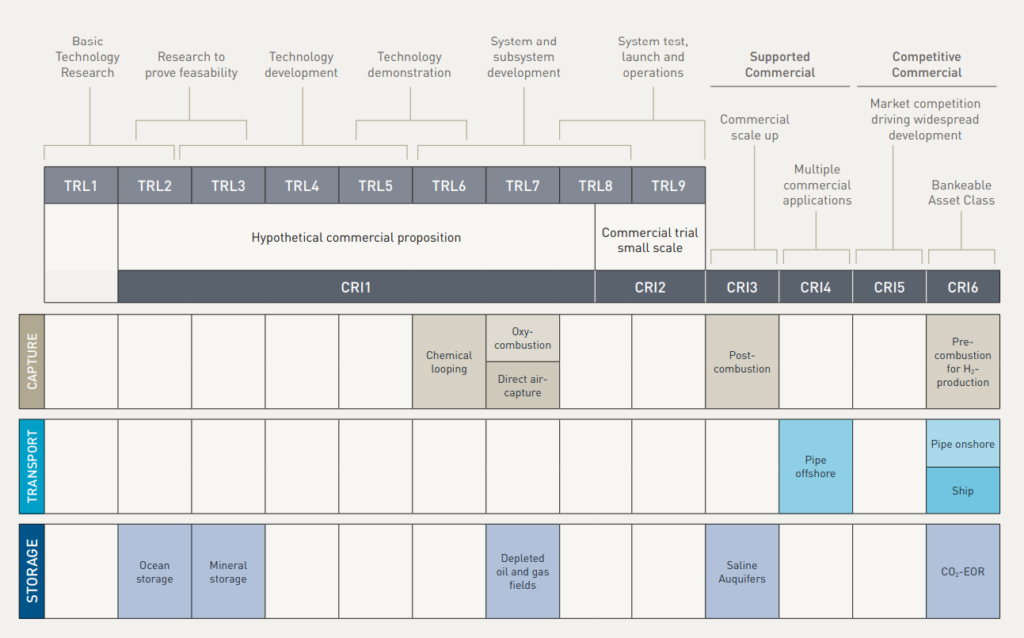
Figure 10: Evaluation of the maturity of CCS technology elements. From “Potential for reduced costs for carbon capture, transport and storage value chains (CCS)”, DNV GL, 2019. Report No.: 2019-1092, Rev. 2
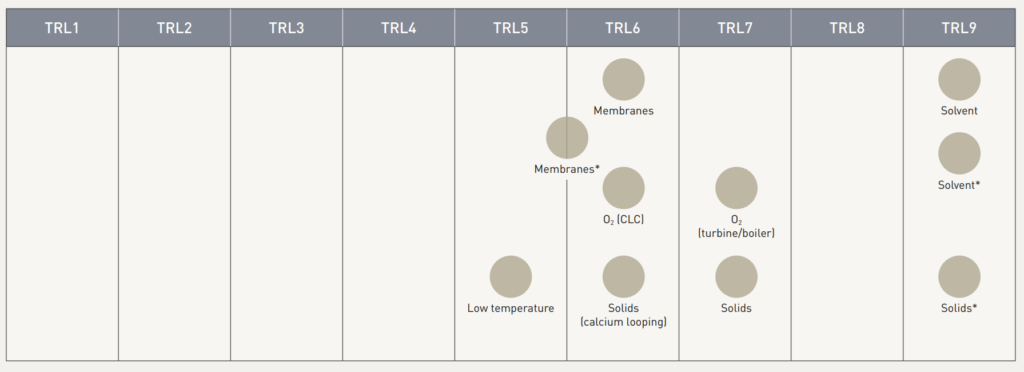
Figure 11: Technology readiness level for different CO2 capture technologies. Technologies used for hydrogen production at pressurized conditions are denoted with *. From “Technology status for CO2 capture, transport and storage”, Gassnova, 2019.
Using an independent third party to perform or to verify the technology qualification may be an efficient way to define and execute an unbiased qualification program.
Figure 10 shows the maturity of various technology elements relevant to CCS in terms of Technology Readiness Level (TRL) and Commercial Readiness Index (CRI), as evaluated by DNV GL in a study for Gassnova. The TRL is a measure used to rank different technologies according to their history of demonstration and qualification, while the CRI is a complement to TRL to assess commercial maturity.
The transport part of the CCS chain is considered to be the most mature. For the storage part the maturity levels are very dependent on the storage type/site. For capture technology, the maturity varies a lot depending on both the type of technology and the application, as further shown in Figure 11.
Technology qualification should be risk based and build on the precautionary principle. Key elements are typically:
- Strategy for technical fall-back options
- Technology vendor alternatives
- Evaluate QA system at vendor
- Third-party assessment of available documentation
- Mapping in-house competence (on the buyer side)
- Evaluate reference cases: recent, reliable, relevant; duration and size
- Identify areas where the intended application represents a step-out from previous experience/references
- Plan and perform pilot testing, if needed
- Assess availability tools and methods needed for the qualification, e.g. related to HSE properties of solvents
Use of recognized standards for technology qualification has proved extremely It has helped companies that have less experience with technology qualification to work systematically with new technology. A common structure and methodology also made the technology qualification by Heidelberg Materials and Fortum Oslo Varme more transparent, which made it easier for Gassnova to evaluate their deliverables from the concept and FEED studies.
TRL is often assigned based on the least mature part of the technology, which makes the readiness level alone unsuitable as a measure for how much work is needed to qualify the technology. Developing a technology qualification program will identify the time and resources needed to qualify a technology.
Both Heidelberg Materials and FOV used DNV GL as an independent third party to verify their technology qualifications. Upon completed verification DNV GL issued “Statement of qualified technology” for the different technologies that were qualified. The involvement of such a third party aided the technical discussions between Gassnova, the industrial partners, and the technology providers.
Throughout the project development, Gassnova has maintained the position to encourage use of proven technology, unless the benefit of using new technology elements significantly outweighs the risks.
For the transport and storage part of the project, Northern Lights intends to utilize standard and proven technology used in the CO2 industry. Only minor uncertainties have been identified during the technology maturity mapping process in the FEED phase.
For the capture part of the project, both Fortum Oslo Varme and Heidelberg Materials will use technologies that are unproven in the intended applications; first and foremost they have executed qualification programs for their respective amine technologies, but Heidelberg Materials has also qualified a CO2 compressor with heat recovery and waste heat recovery units (WHRU).
For both companies, it has been important to verify and document that their selected capture technologies will allow them to operate within Norwegian emissions regulations.
Amine capture technology is based on a chemical reaction between the amine solvent and the CO2 in the flue gas. Central questions regarding the use of this kind of technology are related to how much CO2 will be absorbed in the amine, how aerosol content in the flue gas will affect carry-over and emission of amines, which chemical species the amine may degrade into, how fast the degradation occurs, etc.
In the planning of the now cancelled Norwegian full-scale CO2 capture project at Mongstad (CCM), emissions to air of possibly carcinogenic substances related to amines were flagged as a potential showstopper. In 2008, a comprehensive research programme was initiated to identify and close knowledge gaps with respect to the formation of potential carcinogenic substances and the toxicity level of these substances, known as nitrosamines and nitramines. The work resulted in the development of rigorous methods to evaluate these effects. Several amine technology vendors and projects, including the two capture projects in Longship, have used these methods to evaluate their technology*.
After completing their concept study in 2018, Fortum Oslo Varme selected the Shell amine capture technology. This technology has a reference plant in the Boundary Dam facility in Canada, operated by Sask Power. The Boundary Dam flue gas differs from the flue gas found at Fortum Oslo Varme’s waste-to-energy plant and it is also operated under less strict emission requirements than will be the case in Norway. To verify amine emission level, solvent degradation and energy efficiency, Fortum Oslo Varme designed, installed and operated a custom-made pilot plant for the Shell capture technology (DC-103 solvent). Based on the test results from the pilot, the technology was deemed qualified for use at the operating conditions and flue gas composition expected at the waste-to- energy plant.
Heidelberg Materials screened various capture technologies before selecting the amine- based technology from Aker Solutions (now Aker Carbon Capture) before starting the feasibility study late 2015. The technology had already been qualified for the CCM project at Mongstad, partly through testing at TCM. However, to establish the actual capture performance and expected amine emission levels with the flue gas in Brevik, Heidelberg Materials required a pilot test at their cement plant. The early phase of Heidelberg Materials’s technology qualification programme was funded by the CLIMIT programme, including a test campaign performed by Aker Solution using their Mobile Test Unit (MTU) and covering some 7,400 operating hours.
* More info on the “tool-box” and qualification methods developed for the CCM-project can be found at ccsnorway.com/hse-studies/
It has been possible to develop the CCS chain with limited use of new technology, and only the amine technologies used for capture of CO2 have had no fallback
Reference cases used as ”evidence” in technology qualification must be scrutinized to assure relevance. According to DNV-RP-A203, “Only knowledge and experience that is documented, traceable and accessible to the qualification team should be used”. This understanding has been at the heart of the capture technology qualification done by both Heidelberg Materials and Fortum Oslo Varme, where it has been crucial to verify the amine degradation and emissions to air.
The experience with qualification of amine technology during the CCM project has been valuable in the development of Longship. Fortum Oslo Varme, Heidelberg Materials and Yara, as well as their technology providers and engineering companies, have used the tools, methods and expertise developed around the CCM project in their processes to select and qualify capture technology.